HPC Introduction
■ Machine Tool Coolant Pressure Level Introduction
Low Pressure Systems | Under 10 Bar ( 150 PSI ) |
Output of coolant pumps on general machine tools. |
---|---|---|
Medium Pressure Systems | 20 ~ 60 Bar ( 300 ~ 900 PSI ) |
Moderately improve cycle time and tool life. |
High Pressure Systems | 70 ~ 100 Bar ( 1,000 ~ 1,500 PSI ) |
Achieve optimal cycle time, tool life, efficiently machine hard to cut materials, and also have the better chip solution. |
Ultra-High Pressure Systems | Above 100 Bar ( 1,500 PSI ) |
Utilized in machining super alloys and ultra-hard to machine materials. |
■ Machining Effects
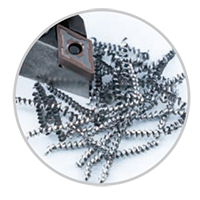
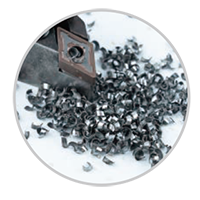
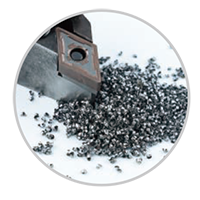
■ Coolant Pressure Case Studies
Mill Application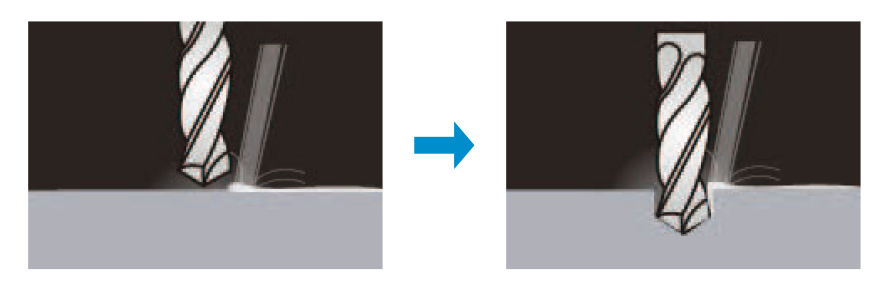
Low Pressure
Tool need to be retracted while milling to clean out the chips.The whole process takes lots of time.
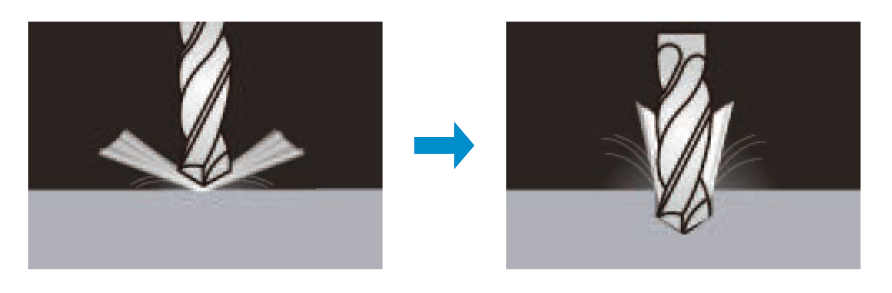
High Pressure
Coolant can hit directly to the milling spot and clean out all the chipsat once. The whole process is much efficient and faster.
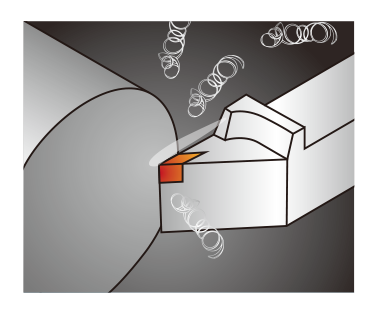
Low Pressure

High Pressure
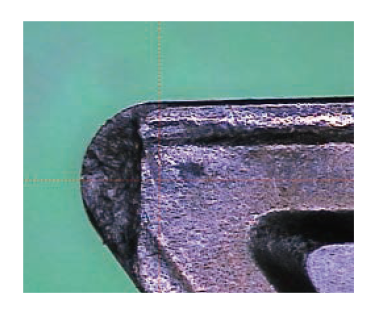
Low Pressure
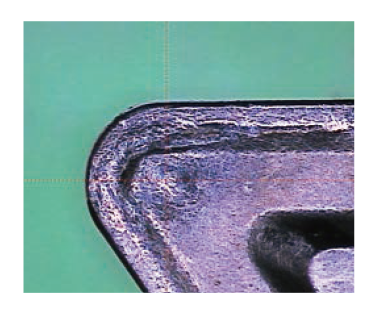
High Pressure
■ High Pressure Coolant System Advantages
If a machine tool is not equipped with a HPC system, the only way to achieve a fraction of the benefits listed below is to design a machine with the structural rigidity to withstand the use of larger motors and faster spindles, this would dramatically increase machine cost by 50% to 100%. Just like the car engine upgrade with Turbo, Adding a HPC system to your machine tool is the simplest and most cost effective way to improve both the cutting feed rate and machine tool production. It also provides a better surface finish and reduces manufacturing cost with extended tool life.
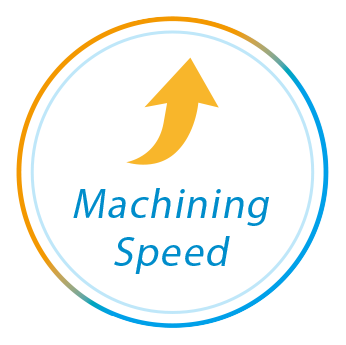
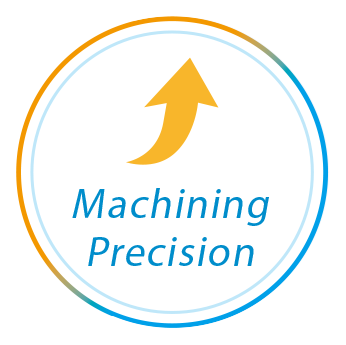
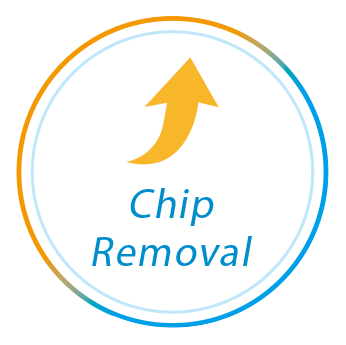
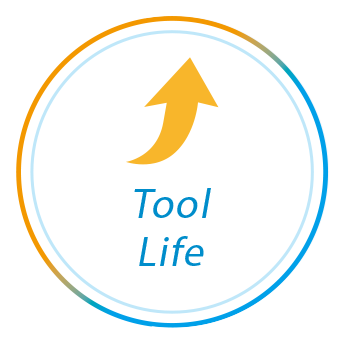
Cutting speeds can be increased up to 20% or more.
Reduce machining cycle time up to 70%.
Improved cutting accuracy with excellent surface finishes.
Excellent in deep-hole machining with best chip removal capability.
Extend tool life up to 25% to 400%.
Breakthrough the vapor barrier for tool-tip heat removal.
■ What is Vapor Barrier?
During machining, temperatures on the tool-tip can reach well over 212 degrees Celsius. When medium to low pressure coolant is used, the high temperature surrounding the tool-tip turns coolant into vapor, thus forming a vapor barrier that blocks coolant from reaching the tool-tip. This barrier leads to poor heat removal causing fast tool wear and poor surface finish. Tests show that HPC systems with outputs above 70 Bar ( 1,000 PSI ) will break through the vapor barrier for effective cooling.
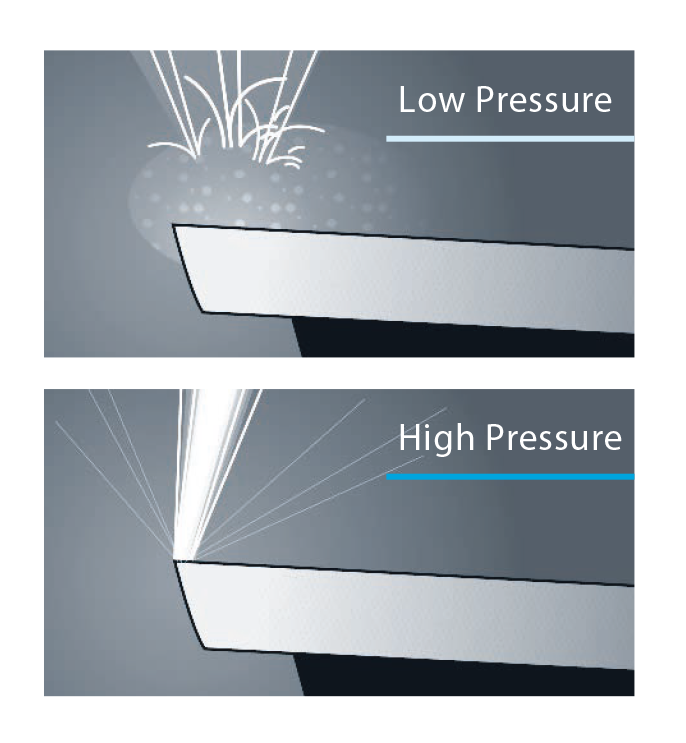
■ The Advantages of AllCool High Pressure Coolant Systems
Average High Pressure Systems | Allcool High Pressure Systems | |
---|---|---|
Filtration systems | Replace the filter within 1 ~ 3 weeks | V Replace the filter bag about 1 ~ 2 months ( Expendables are also cheaper ) |
Pressure detection | Mechanical type | V Electronic type ( High accuracy and long expired date ) |
Coolant level detection | Mechanical type | V Electronic type ( Low failure rate and good stability ) |
High pressure pump | Gear pump | V Diaphragm pump ( High tolerance of dirt entry and regardless oil-water ratio ) |